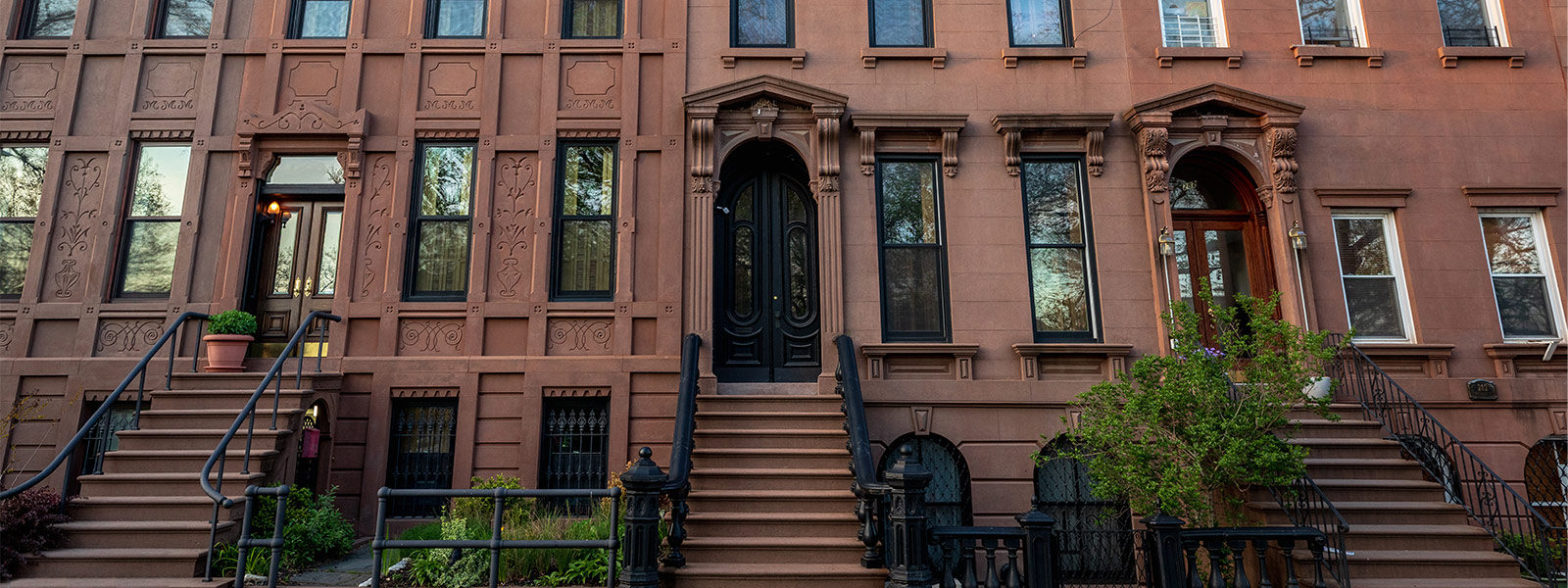
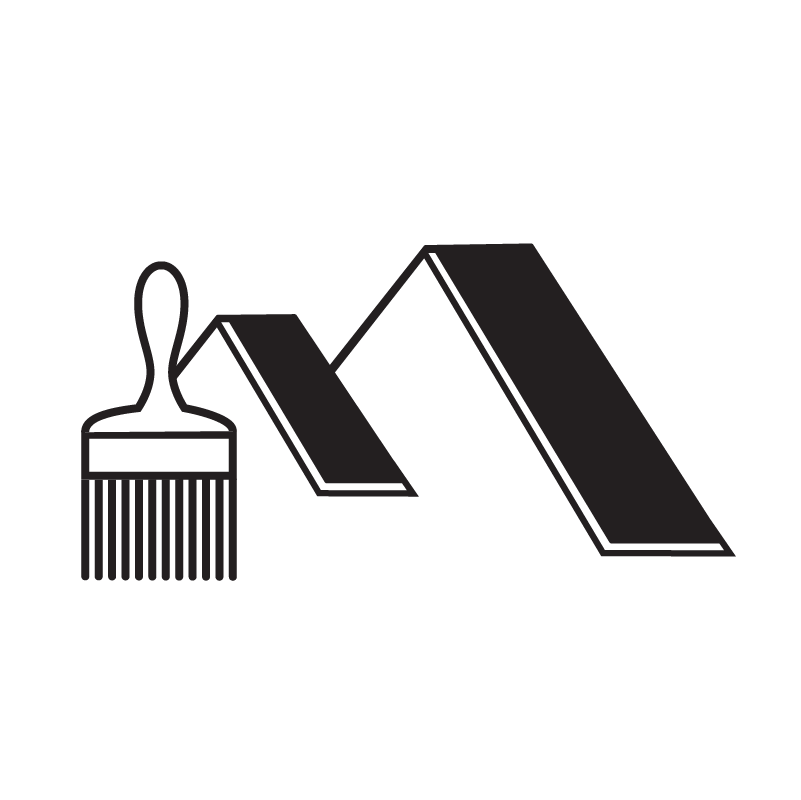
What are Brownstones?
Brownstone renovations are our core business. When people think about New York City, they think primarily about two types of architecture. Skyscrapers and Brownstone townhouses. These Rich patina buildings have several distinguishing design elements: The homes mostly start a few feet off the street, atop staircases adorned by various banister carvings. These designs add to the regal nature of the houses and contribute to the high prices they fetch in the NYC real estate market.
How did Brownstone become such a popular choice for the 19th-century New York Real estate market?
Brownstone is a brown Triassic–Jurassic sandstone that was historically a popular building material. The term is also used in the United States and Canada to refer to a townhouse clad in this or any other aesthetically similar material. (Wikipedia) The stone is pink when first cut but changes its color to a deeper brown color once it has been exposed to the air.
The 19th century was an age when Americans were interested in Neo-Classicism as a form of architecture. The Industrial Revolution had by then ushered in a widespread streamlining of production — the construction industry invented new production methods, and many began erecting new buildings quickly. Romantic Classicism was a response to the pace of urbanization, a reminder that nature was not only necessary but desirable. Brownstone was the happy marriage of these two worlds. Steam-powered machines let laborers cut and shape brownstone faster and more cheaply than ever before, making it affordable — and its organic hues recalled the beauty and power of the wild. Brownstone was the way to go for middle-class townhouse and rowhouse owners who wanted a taste of luxury. For little money — far less than what it might cost with limestone, granite, or marble — a homeowner could have a six-inch brownstone façade built, complete with a stoop, a rising staircase, and whatever lovely carved accouterments they desired. (StreetEasy)
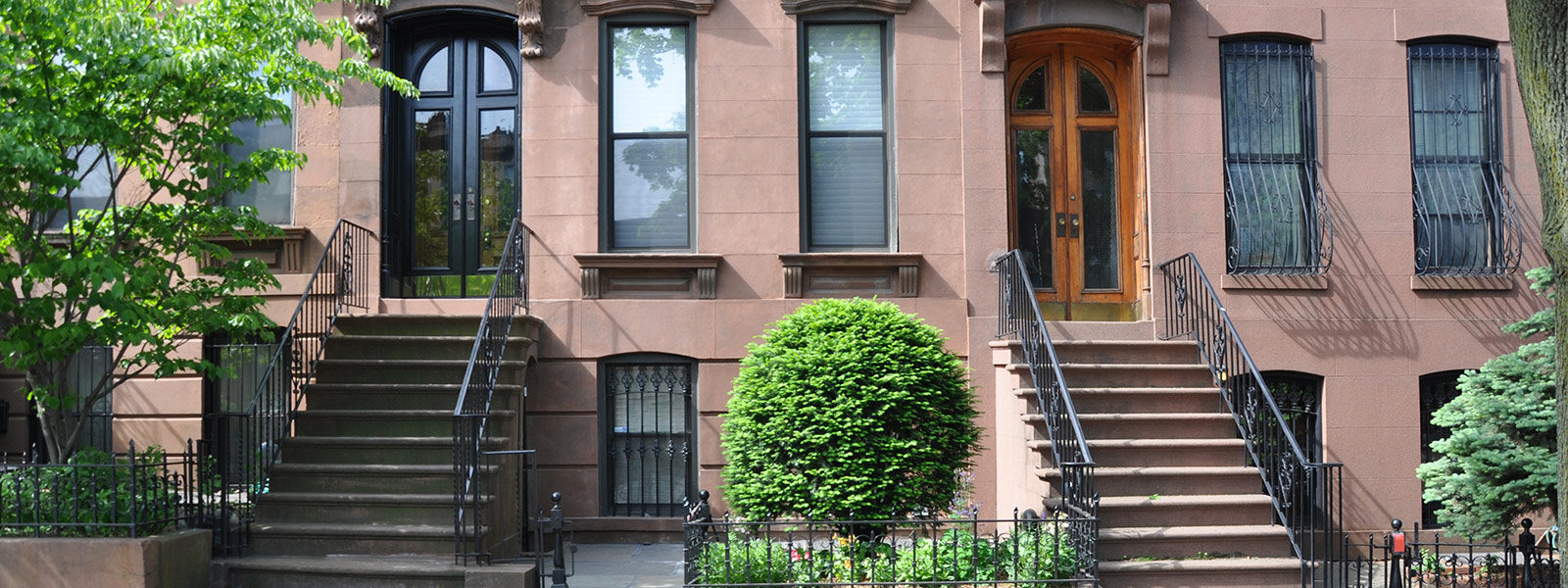
Why do Brownstone buildings deteriorate?
Brownstone was deemed “not really much good as a building material” by Vincent Scully, professor emeritus of the history of art at Yale University.
Brownstone was popular because it is unusually easy to carve and quarry, but these qualities also made houses clad in it susceptible to weathering and damage over time. (Wikipedia)
The main reasons for damage are: (Brownstoner Guide)
- Exfoliation – Separation, and failure of stone along its sedimentary bedding planes.
- Contour scaling – Failure of a thin surface layer of the stone parallel to the worked surface of the stone, rather than along its bedding planes.
- Disaggregation – Loss of cohesion between sand grains as the binder deteriorates
All of these types of deterioration are caused by exposure to air and climate. Therefore, the only way to keep the building is to keep a vigilant schedule of maintenance and protection.
If you own or live in a Brownstone, you can reduce the overall building repair costs by providing proper maintenance. A regular maintenance schedule can reduce water infiltration and slow the rate of decay.
The Brownstoner website suggests taking the following Brownstone maintenance protocol:
- Clear gutters regularly – Clean your gutters a few times a year to make sure your gutters allow free flow of water
- Maintain your roof – Repair all leaks and drainage systems quickly and effectively.
- Remove vegetation – Ivy buildings look great, but the plants attach themselves to the stone and absorb minerals from it, weakening the structure.
- Fill open joints – Caulk around windows and doors. It prevents moisture infiltration.
- Maintain Flashing – Use non-corrosive sheet metal to cover the open gap between the stone elements.
- Repoint when necessary – Hire a qualified mason to repoint the building as required.
- Clean carefully – Unprofessional cleaning can damage the building. Hire a professional mason to clean the building every few years and make sure that they don’t use any harsh chemicals on the building. Gentle soap and non-ionic detergent are the best options for this task.
One of the most prominent ways to maintain your Brownstone would be to resurface after a rigorous and in-depth examination by a Brownstone specialist.
One of the most prominent ways to maintain your Brownstone would be to resurface after a rigorous and in-depth examination by a Brownstone specialist. According to Landmarks Preservation Commission, the resurfacing procedure is as follows:
1. Preparation of the surface
Use a toothed chisel to cut back all deteriorated surfaces to be repaired to a sound base, removing all loose stone to provide a rough surface.
2. Mechanical keying
To create a mechanical key or holding mechanism for the patch, undercut the edges of the patch to form a fine dovetail. Then, drill holes 1/2 inch in diameter and 1/2 inch deep, spaced 2-3 inches apart in staggered rows.
You must vary the angles.
3. Surface washing
Wash the prepared surface with water and a soft brush.
4. Slurry coat
Apply a thin slurry coat with a brush and rub vigorously into the surface.
The slurry coat consists of material in the following mix by volume:
Slurry coat
One part white Portland.
Two parts type s lime.
Six parts sand.
Mix with water.
5. Scratch coat
The first scratch coat must be pressed into the slurry coat while the slurry is still moist. Each scratch coat must be scored before initial drying to provide a key for the following coats. No coat should exceed 3/8 inch in thickness. Allow 2-4 hours between scratch coat applications.
Scratch coats consist of material in the following mix by volume:
1 part white Portland cement
1 part type s lime
6 part sand
Mix with water.
6. Finish coat
The finish coat is applied once the patch has been built to the required thickness. Only this last coat is formulated to match the color and texture of the stone being repaired. The finish coat should be formulated as follows:
1 part white Portland cement
1 part type s lime
2-3 part sand
3-4 part crushed stone
Dry pigments. Mix with water.
All measurements are parts by volume.
All ingredients must be combined dry and then mixed with potable water.
7. Surface finishing
The surface must be finished to match the original stone tooling, or existing condition. Possible surface treatments include damp sponging (stippling), dry toweling with a wooden oat, and acid etching with diluted hydrofluoric acid. All treatments are executed while the patch is partially cured to leather hardness.
Curing time is also needed in between different periods.
If you want more information about maintaining your Brownstone, don’t hesitate and call Z. Abedin constructions at 718-633-9605, or just use our contact form.